Plastic Manufacturing ERP Software streamlines operations within the demanding plastic manufacturing industry. These systems integrate various aspects of the business, from raw material procurement and inventory management to production scheduling, quality control, and sales order processing. Effective ERP implementation can significantly improve efficiency, reduce costs, and enhance overall profitability by providing real-time data and insightful analytics across the entire production lifecycle.
This allows businesses to make data-driven decisions, optimize processes, and gain a competitive edge in a rapidly evolving market.
The software’s capabilities extend beyond basic operational management. Advanced features often include robust reporting tools for financial analysis, supply chain visibility, and customer relationship management (CRM) integration. This holistic approach allows businesses to gain a comprehensive understanding of their operations and make strategic decisions to improve performance and growth. The selection and implementation of the right ERP system is crucial for success, requiring careful consideration of the specific needs and challenges of the plastic manufacturing environment.
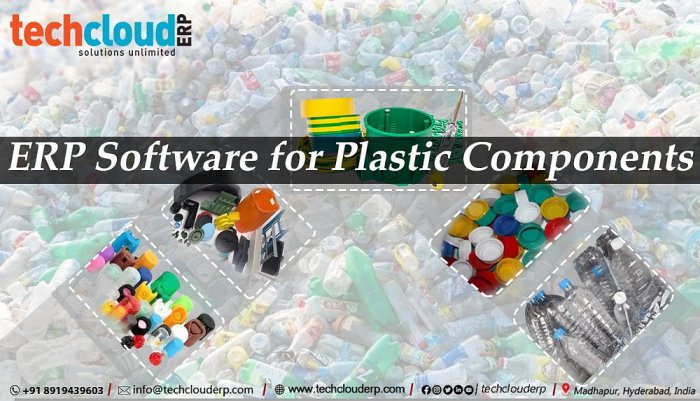
Source: wixstatic.com
The plastic manufacturing industry is a dynamic and competitive landscape, demanding efficiency, accuracy, and responsiveness to thrive. Enterprises Resource Planning (ERP) software offers a powerful solution to streamline operations, improve profitability, and gain a competitive edge. This comprehensive guide delves into the intricacies of plastic manufacturing ERP software, exploring its functionalities, benefits, implementation considerations, and future trends.
Understanding the Needs of Plastic Manufacturers
Plastic manufacturing presents unique challenges. From managing complex raw material sourcing and intricate production processes to tracking inventory and meeting stringent quality control standards, the operational complexity is significant. Traditional methods often fall short, leading to inefficiencies, increased costs, and potential delays. This is where plastic manufacturing ERP software steps in to provide a centralized, integrated system to manage all aspects of the business.
Key Challenges Addressed by ERP:, Plastic manufacturing erp software
- Inventory Management: Tracking diverse plastic resins, additives, and finished goods requires robust inventory control, preventing stockouts and minimizing waste.
- Production Planning & Scheduling: Optimizing production schedules based on demand forecasts, material availability, and machine capacity is crucial for on-time delivery.
- Quality Control: Maintaining consistent product quality throughout the manufacturing process, complying with industry regulations (e.g., FDA, RoHS), and minimizing defects are paramount.
- Supply Chain Management: Efficiently managing relationships with suppliers, ensuring timely delivery of raw materials, and optimizing logistics are essential for cost-effectiveness.
- Financial Management: Accurate cost accounting, real-time financial reporting, and effective budgeting are crucial for profitability and informed decision-making.
- Customer Relationship Management (CRM): Managing customer orders, tracking shipments, and providing excellent customer service are key to building strong customer relationships.
Core Functionalities of Plastic Manufacturing ERP Software
A robust ERP system tailored for plastic manufacturing encompasses a wide range of functionalities designed to address the specific needs of the industry. These functionalities typically include:
1. Material Requirements Planning (MRP)
MRP is a core component, accurately forecasting material needs based on production schedules and inventory levels. This prevents shortages, minimizes waste, and optimizes purchasing decisions.
2. Manufacturing Execution System (MES) Integration
Integration with MES provides real-time visibility into the production floor, enabling monitoring of machine performance, tracking production progress, and identifying bottlenecks. This allows for proactive adjustments to optimize production efficiency.
3. Quality Management System (QMS) Integration
Integration with QMS ensures adherence to quality standards, facilitates traceability of materials and products, and helps manage non-conformances. This improves product quality and minimizes waste due to defects.
4. Advanced Planning and Scheduling (APS)
APS capabilities go beyond basic scheduling, employing sophisticated algorithms to optimize production schedules considering various constraints, such as machine availability, material constraints, and due dates. This improves on-time delivery and reduces lead times.
5. Warehouse Management System (WMS) Integration
Integration with WMS streamlines warehouse operations, optimizing inventory storage, picking, and packing processes. This improves efficiency and accuracy in managing inventory.
6. Business Intelligence (BI) and Reporting
Access to real-time data and comprehensive reporting capabilities provides valuable insights into operational performance, allowing for data-driven decision-making and continuous improvement.
Benefits of Implementing Plastic Manufacturing ERP Software
The advantages of adopting a specialized ERP solution for plastic manufacturing are substantial and far-reaching:
- Improved Efficiency: Automation of tasks and streamlined processes lead to significant time and cost savings.
- Enhanced Productivity: Optimized production scheduling and resource allocation maximize output and minimize downtime.
- Reduced Costs: Minimized waste, improved inventory control, and efficient resource management contribute to lower operating costs.
- Better Quality Control: Enhanced traceability and quality management capabilities lead to improved product quality and reduced defects.
- Improved Customer Satisfaction: On-time delivery and high-quality products contribute to increased customer satisfaction and loyalty.
- Increased Profitability: All the above factors combine to boost overall profitability and return on investment.
- Better Decision Making: Real-time data and comprehensive reporting enable data-driven decision-making, leading to strategic advantages.
- Improved Supply Chain Visibility: Enhanced tracking and monitoring of materials and products throughout the supply chain improves responsiveness and reduces risks.
Choosing the Right Plastic Manufacturing ERP Software
Selecting the appropriate ERP system requires careful consideration of various factors:
- Scalability: Ensure the system can adapt to future growth and changing business needs.
- Customization: Consider the level of customization needed to meet specific business requirements.
- Integration Capabilities: Verify compatibility with existing systems, such as MES, QMS, and WMS.
- Vendor Support: Choose a vendor with a strong track record of providing reliable support and maintenance.
- Implementation Costs: Evaluate the total cost of ownership, including software licensing, implementation services, and ongoing maintenance.
- User-Friendliness: Select a system with an intuitive interface that is easy for employees to learn and use.
Implementation Considerations
Successful ERP implementation requires careful planning and execution. Key considerations include:
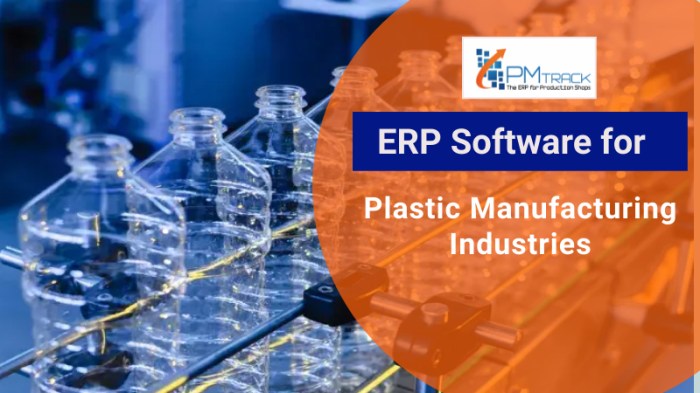
Source: pmtrackerp.in
- Project Planning: Define clear goals, timelines, and responsibilities.
- Data Migration: Develop a comprehensive data migration plan to ensure accurate and efficient transfer of data.
- Training: Provide adequate training to employees to ensure effective use of the system.
- Change Management: Address potential resistance to change and foster a culture of adoption.
- Testing: Thoroughly test the system before going live to identify and resolve any issues.
- Go-Live Support: Ensure adequate support is available during and after the go-live phase.
Future Trends in Plastic Manufacturing ERP
The future of plastic manufacturing ERP is shaped by technological advancements and evolving industry needs. Key trends include:
- Cloud-based ERP: Cloud solutions offer scalability, accessibility, and cost-effectiveness.
- Artificial Intelligence (AI) and Machine Learning (ML): AI and ML are being integrated into ERP systems to enhance predictive analytics, optimize production, and improve decision-making.
- Internet of Things (IoT) Integration: Connecting machines and equipment to the ERP system provides real-time data and enhances operational visibility.
- Blockchain Technology: Blockchain can improve supply chain transparency and traceability.
- Sustainability Focus: ERP systems are increasingly incorporating features to support sustainability initiatives, such as waste reduction and energy efficiency.
Frequently Asked Questions (FAQ)
- Q: What is the cost of implementing a plastic manufacturing ERP system? A: The cost varies significantly depending on the size of the business, the chosen software, and the complexity of the implementation. It’s best to obtain quotes from multiple vendors.
- Q: How long does it take to implement a plastic manufacturing ERP system? A: Implementation timeframes can range from several months to over a year, depending on the complexity of the project and the size of the business.
- Q: What are the key features to look for in a plastic manufacturing ERP system? A: Key features include MRP, MES integration, QMS integration, APS, WMS integration, and robust reporting capabilities.
- Q: Can ERP software integrate with my existing systems? A: Yes, many ERP systems offer robust integration capabilities with other systems, such as MES, QMS, and WMS. However, compatibility should be verified before implementation.
- Q: What is the return on investment (ROI) of implementing an ERP system? A: The ROI can vary, but many businesses see significant improvements in efficiency, productivity, and profitability after implementing an ERP system. The specific ROI will depend on the individual business and its specific needs.
Conclusion
Plastic manufacturing ERP software is a critical tool for businesses seeking to optimize operations, enhance profitability, and gain a competitive edge. By carefully considering the functionalities, benefits, and implementation considerations Artikeld in this guide, plastic manufacturers can make informed decisions to select and implement the right ERP solution to drive their success.
Call to Action
Ready to transform your plastic manufacturing operations? Contact us today for a free consultation to discuss your specific needs and explore how our ERP solutions can help you achieve your business goals.
In conclusion, the adoption of Plastic Manufacturing ERP Software represents a significant step towards modernization and efficiency within the industry. By integrating diverse operational functions, these systems provide a powerful platform for data-driven decision-making, optimized processes, and improved profitability. While the initial investment and implementation can be substantial, the long-term benefits of enhanced efficiency, reduced costs, and improved competitiveness far outweigh the initial challenges.
The key to successful implementation lies in careful planning, thorough system selection, and ongoing employee training and support. Embracing this technology is not merely an option, but a strategic imperative for plastic manufacturers seeking sustained growth and success in today’s dynamic market.
Essential FAQs
What are the key benefits of using ERP software in plastic manufacturing?
Key benefits include improved efficiency, reduced costs, better inventory management, enhanced production planning, improved quality control, and stronger customer relationships.
How much does plastic manufacturing ERP software cost?
Costs vary greatly depending on the size of the company, the specific features required, and the chosen vendor. Expect a range from several thousand to hundreds of thousands of dollars, potentially including implementation and training costs.
What are the common challenges in implementing ERP software in a plastic manufacturing setting?
Common challenges include data migration, integration with existing systems, user adoption, and the need for extensive employee training. Careful planning and change management are crucial for success.
What are some popular ERP software solutions for plastic manufacturers?
Several vendors offer ERP solutions tailored for manufacturing, including SAP, Oracle, Infor, and Epicor. Researching specific solutions that meet your needs is crucial.
How long does it typically take to implement ERP software in a plastic manufacturing company?
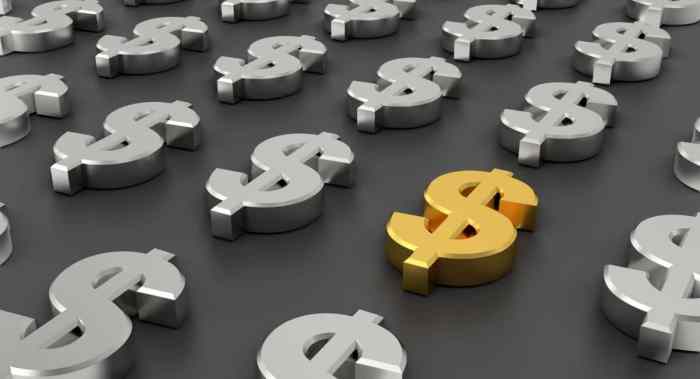
Source: hashmicro.com
Implementation timelines vary significantly based on company size and complexity, but can range from several months to over a year.